Carpenter’s House
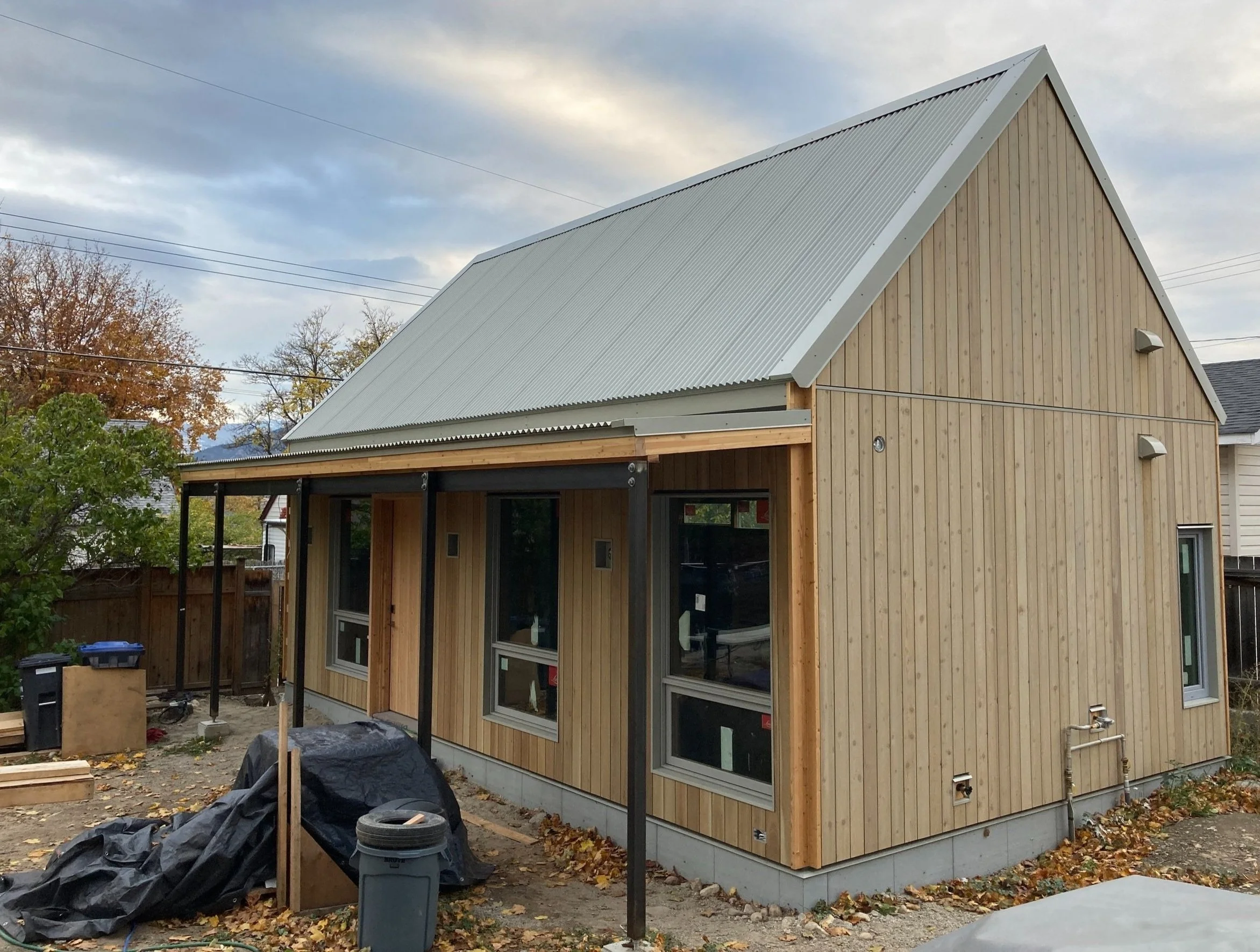
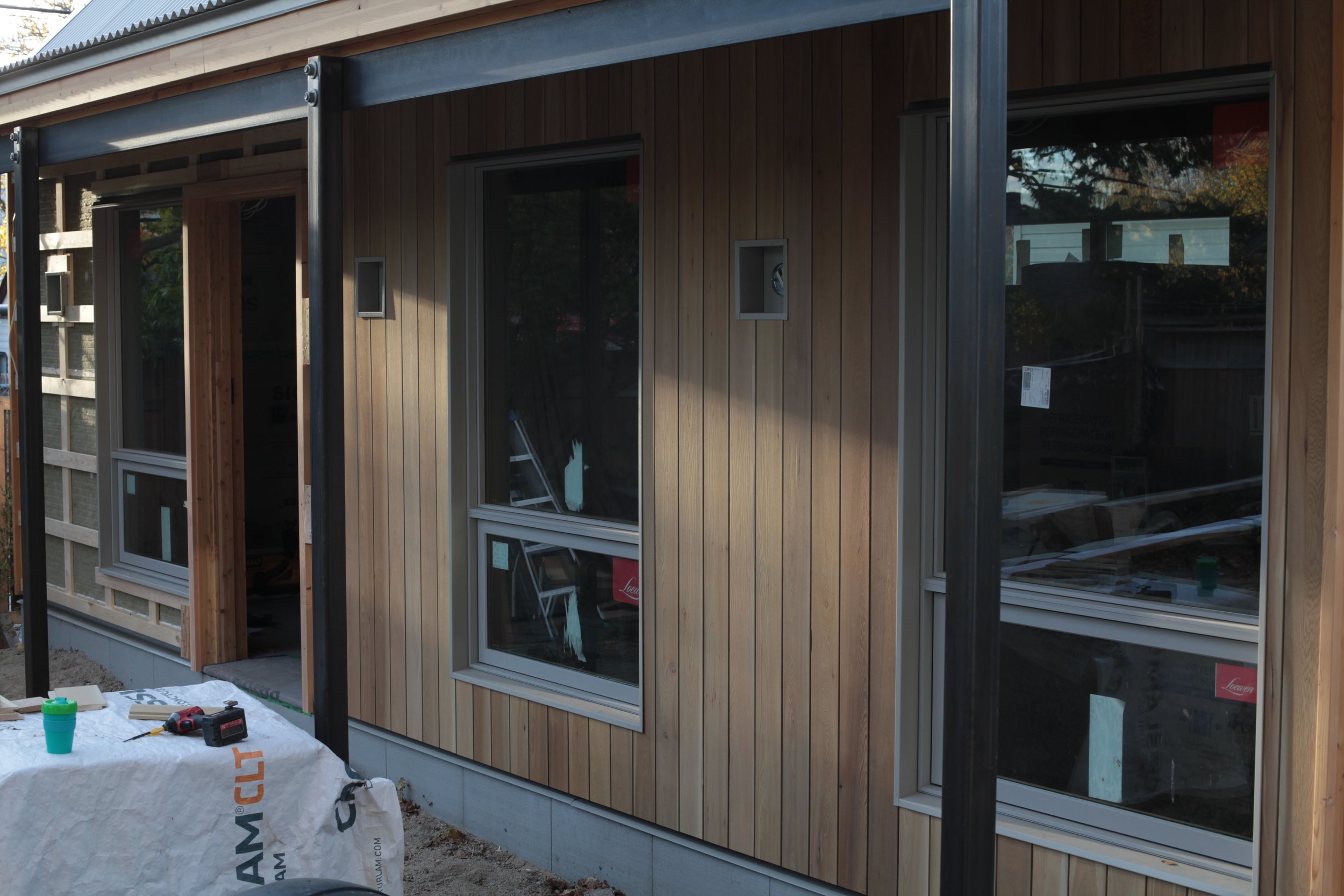
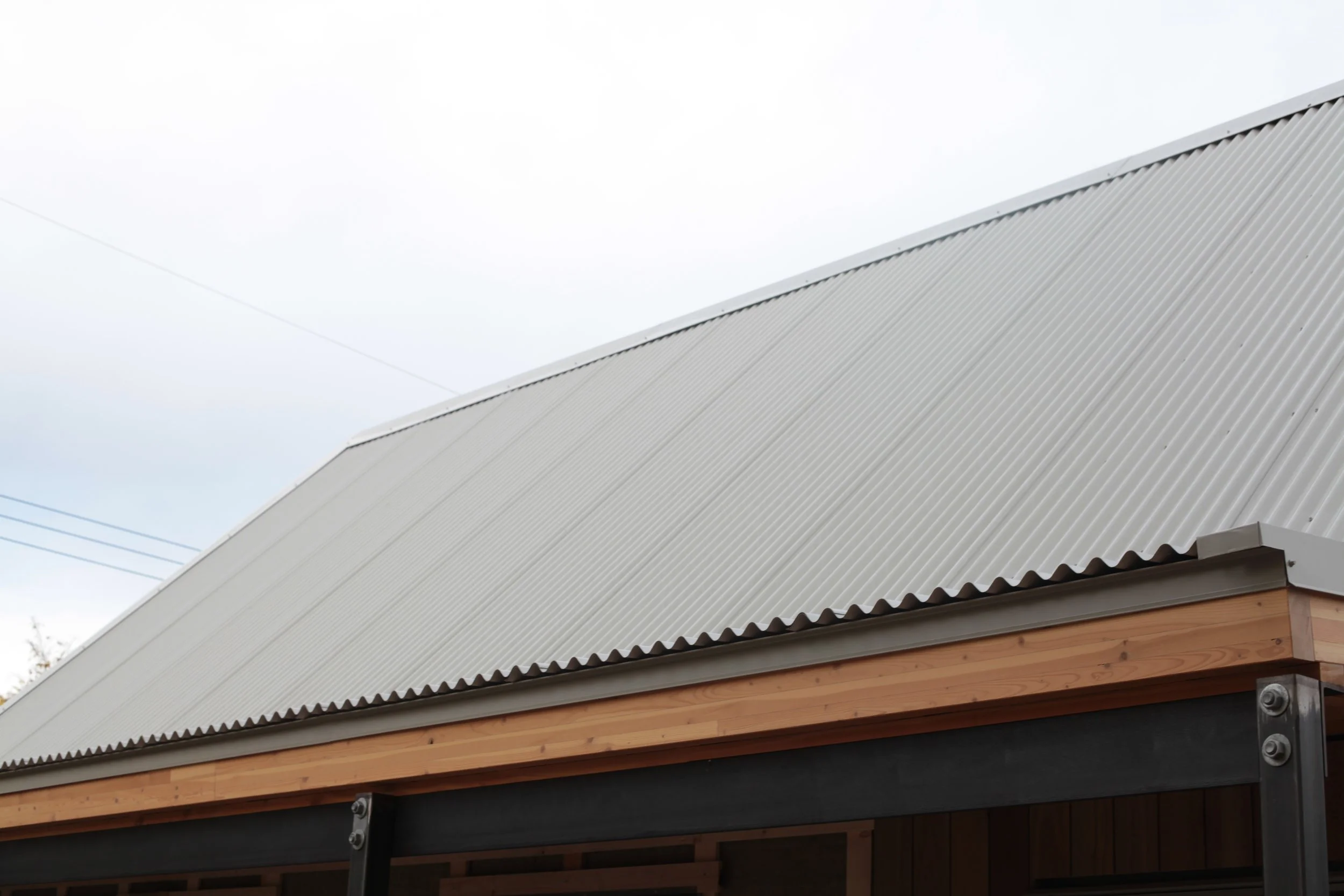
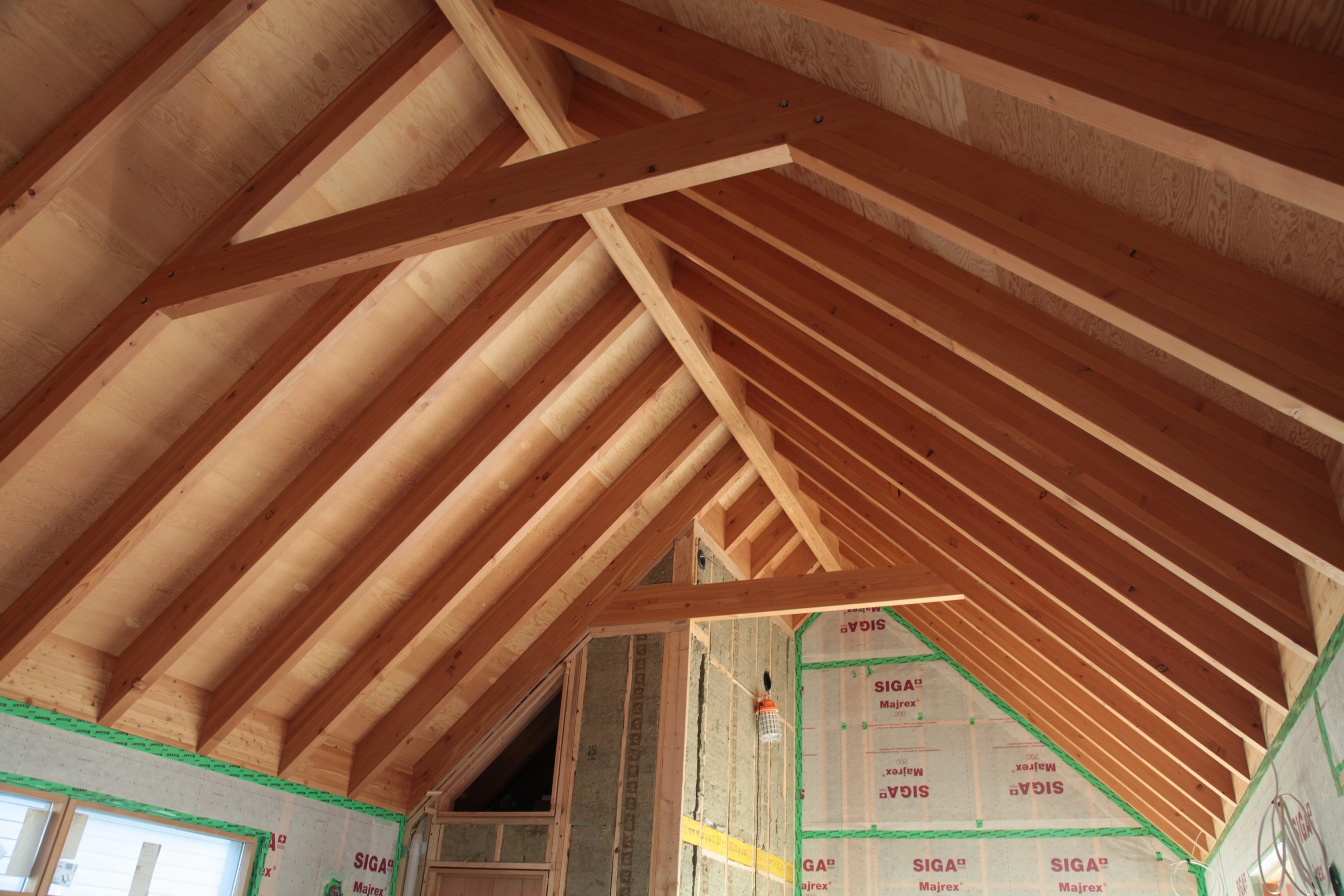
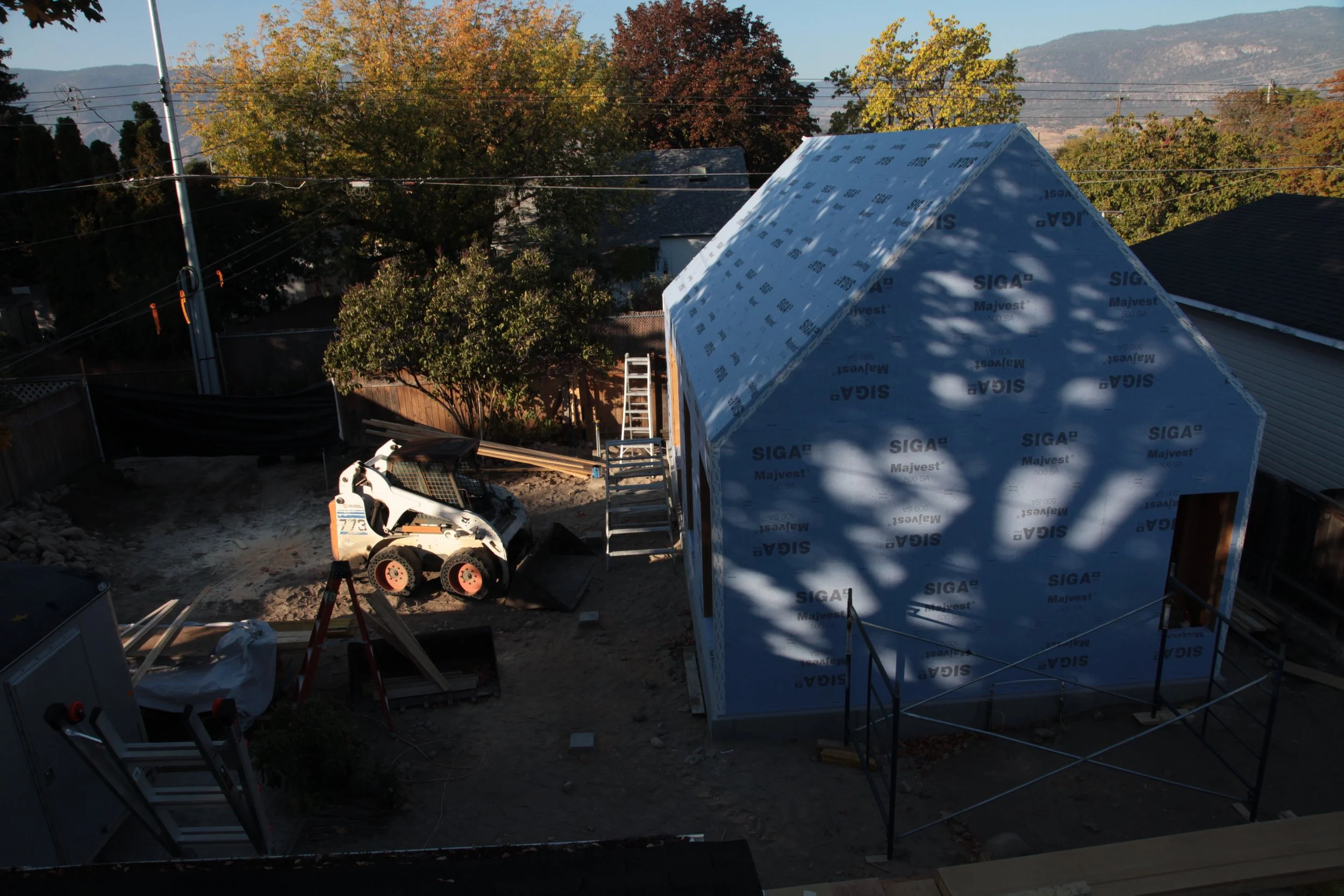
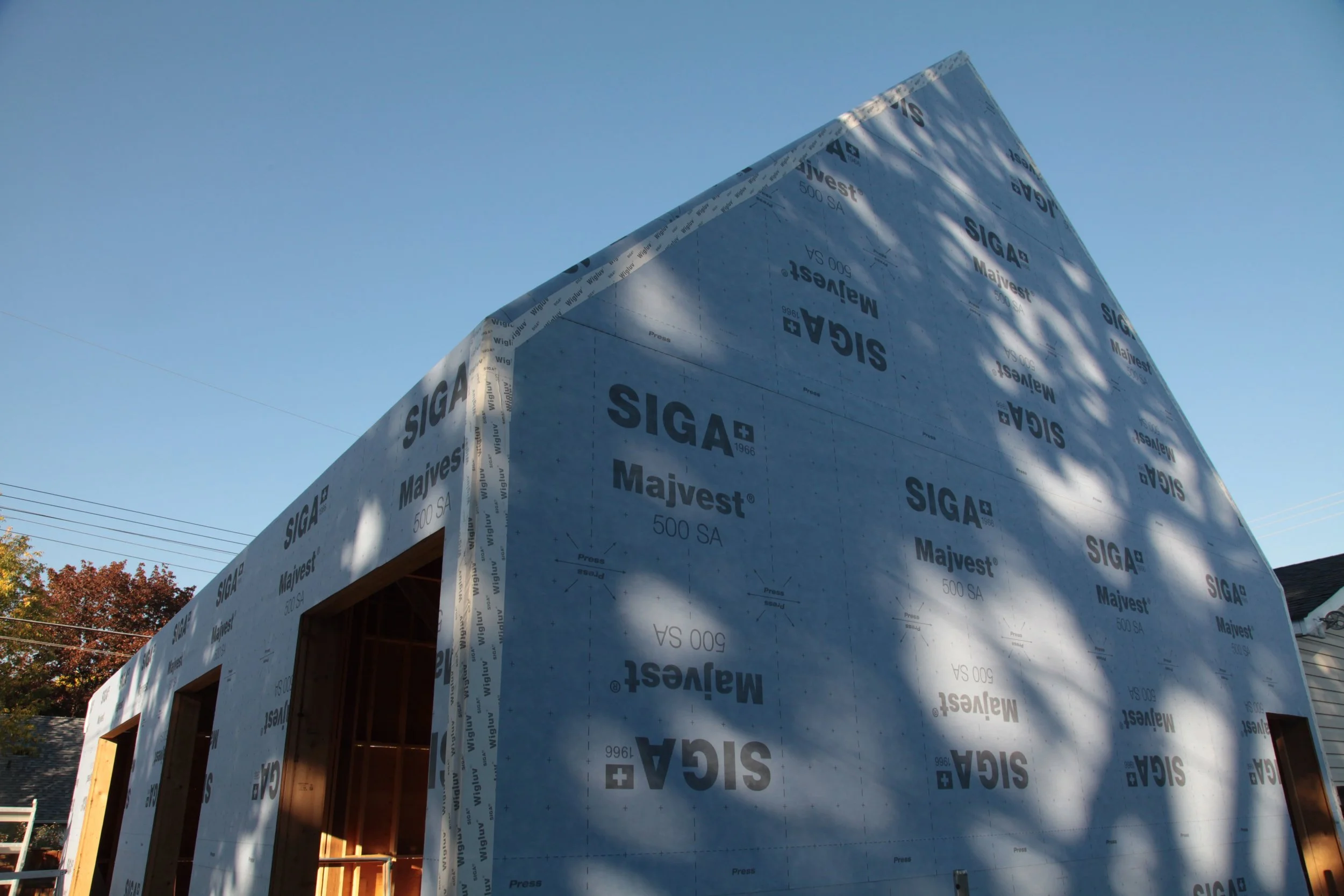

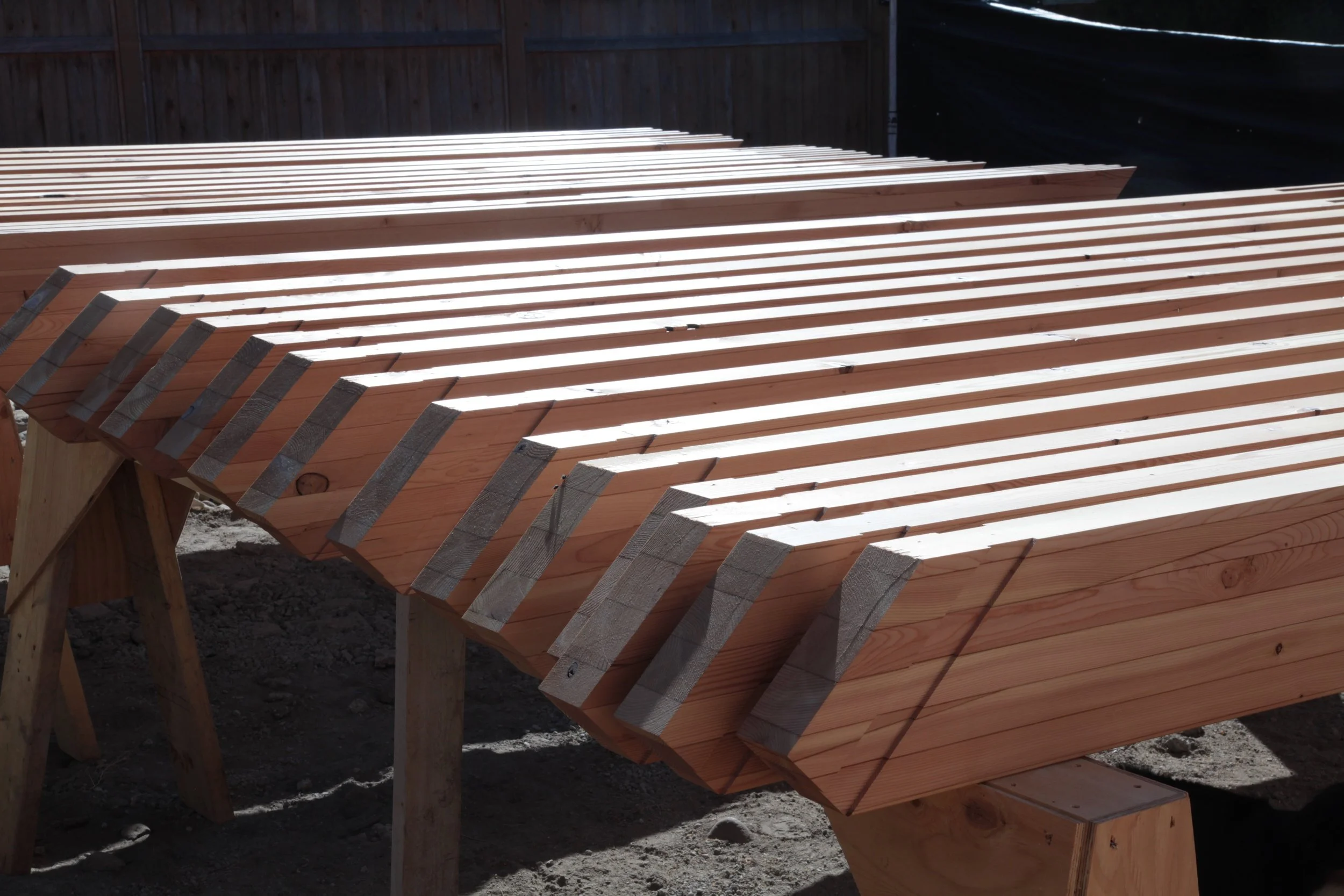

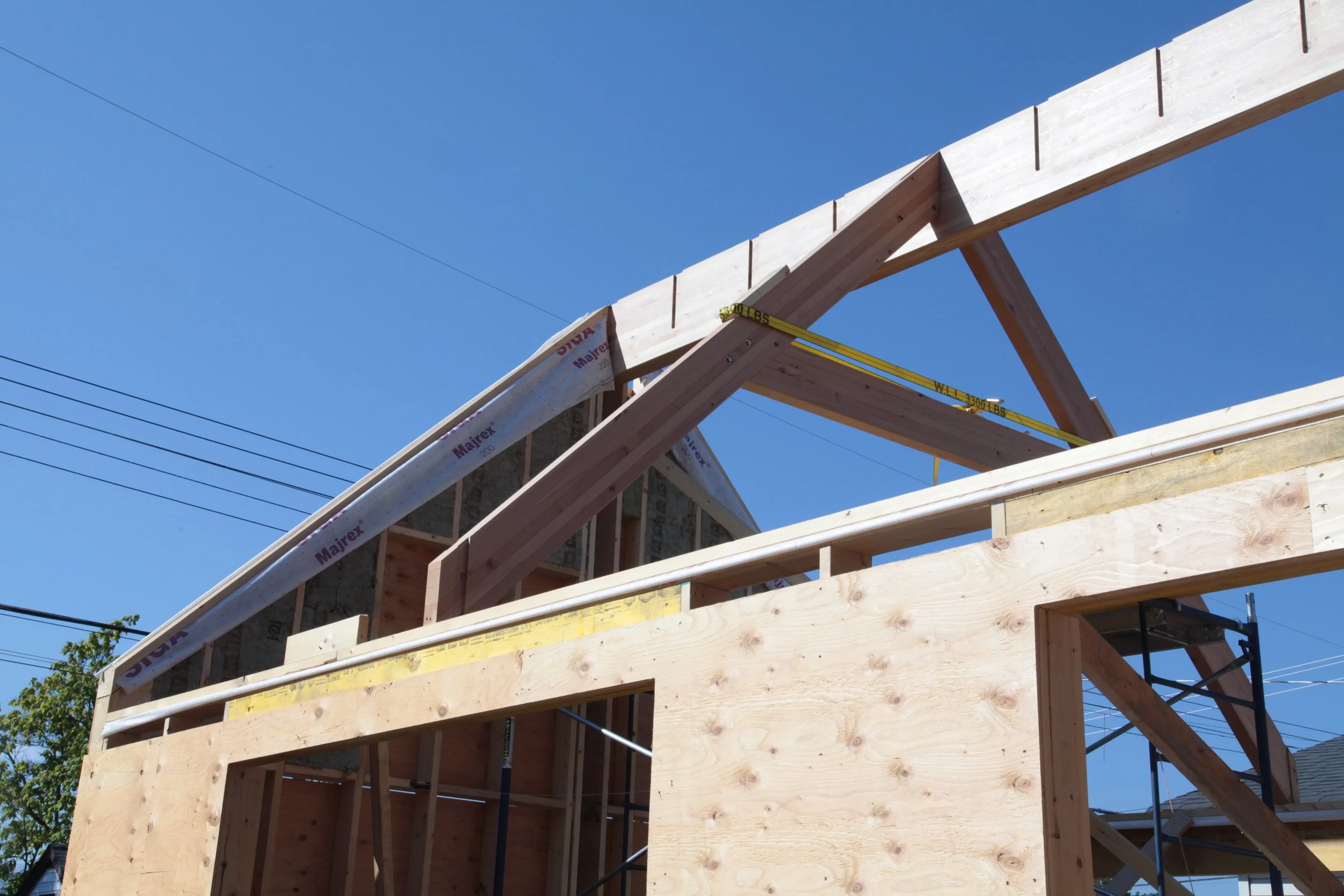
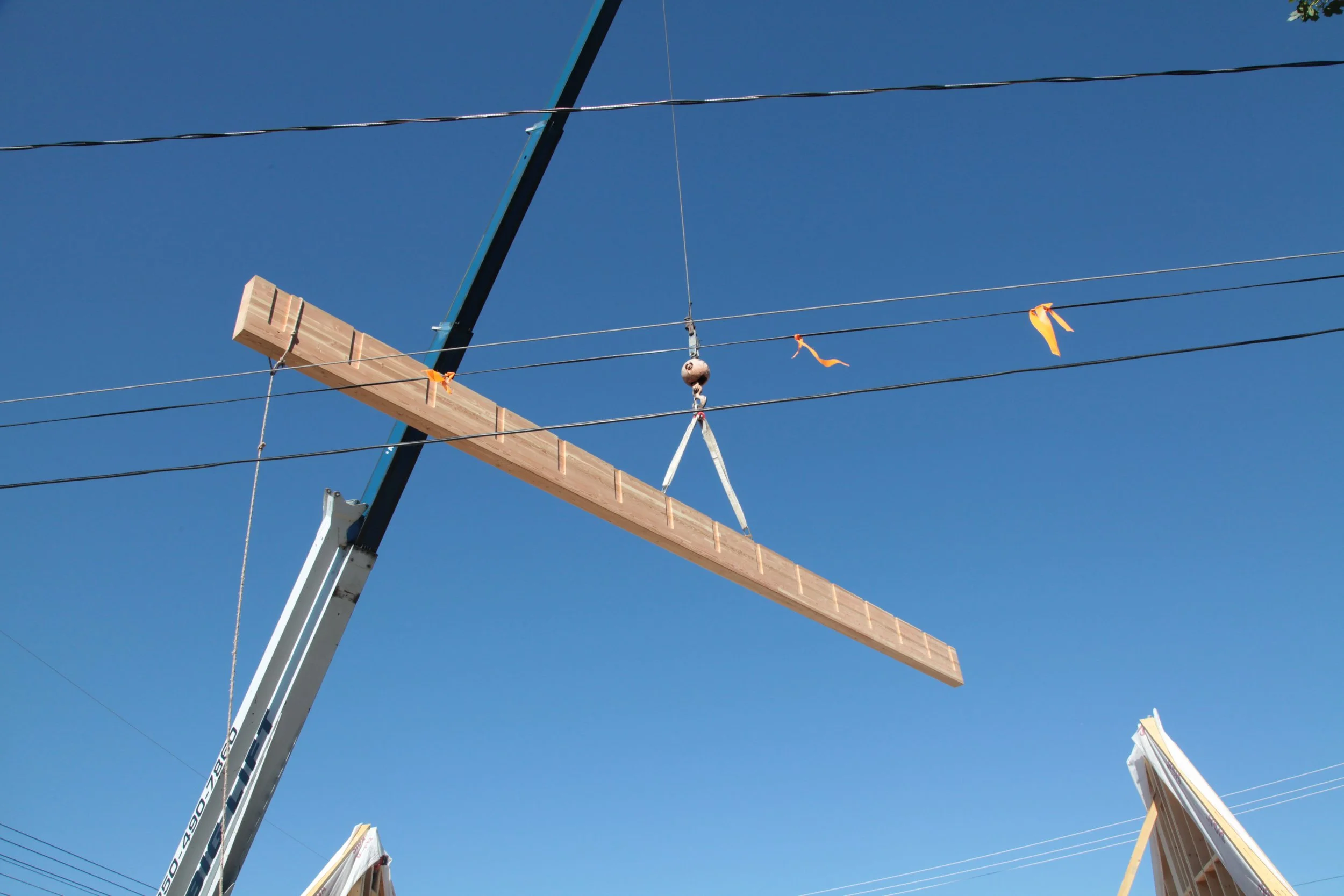
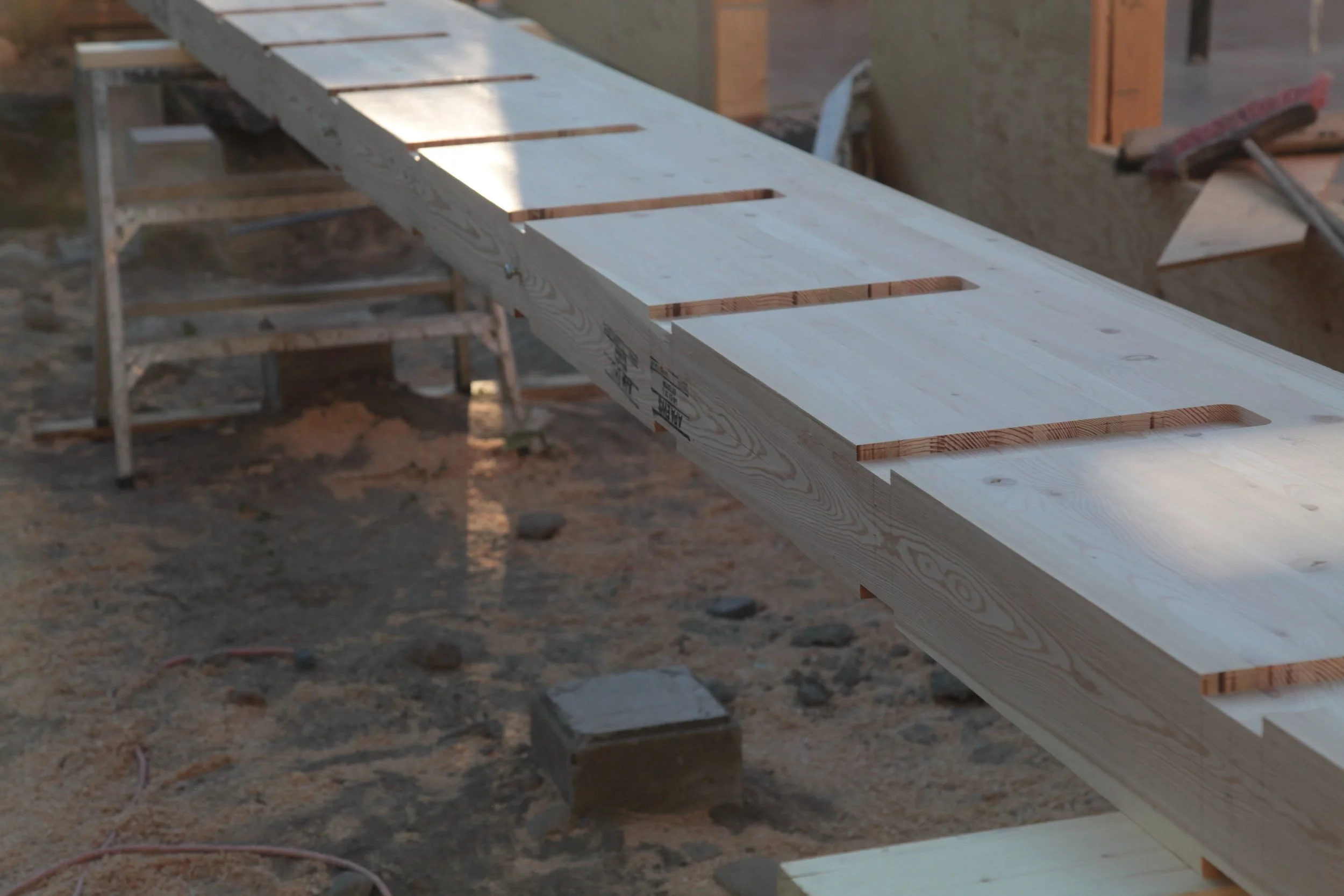
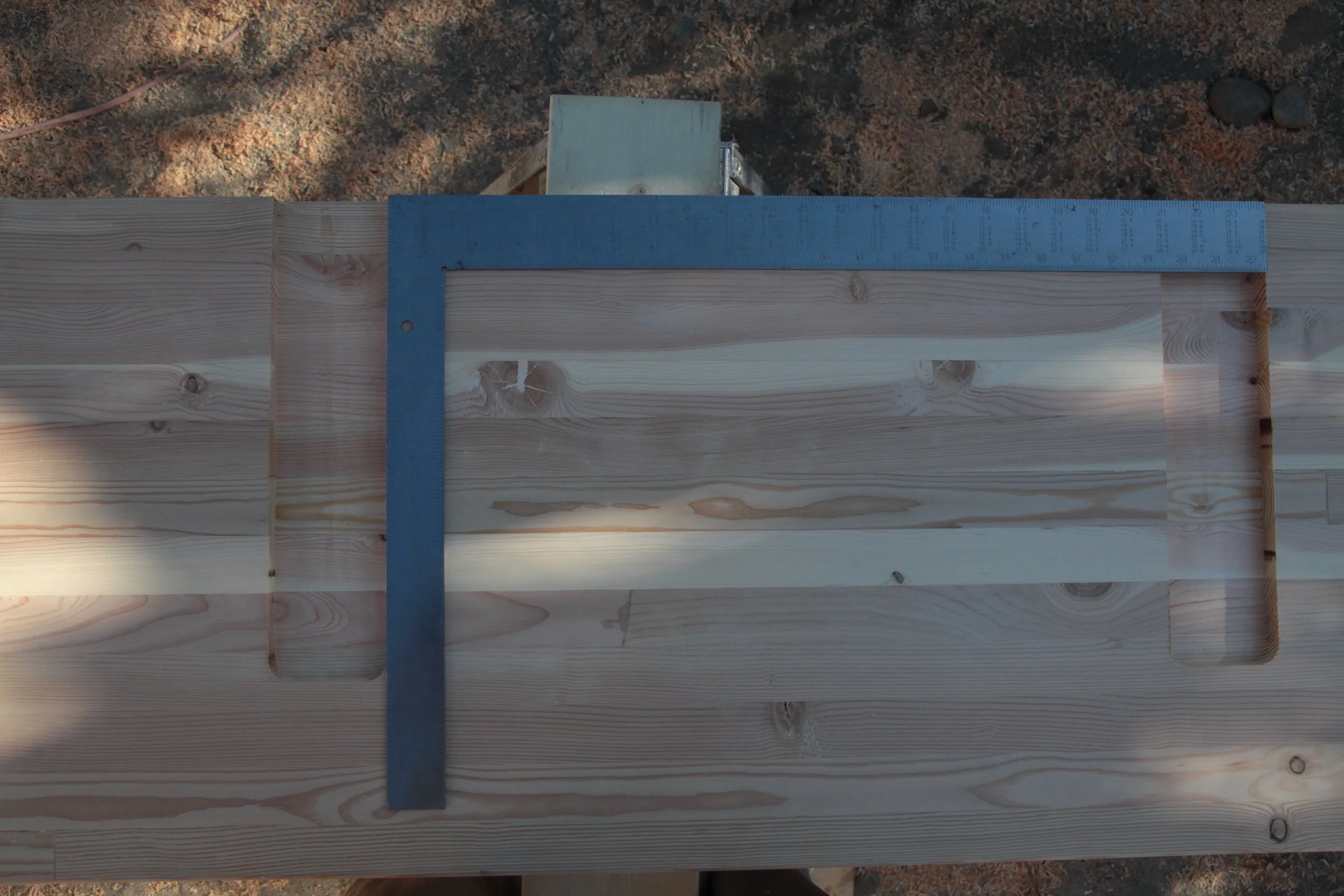
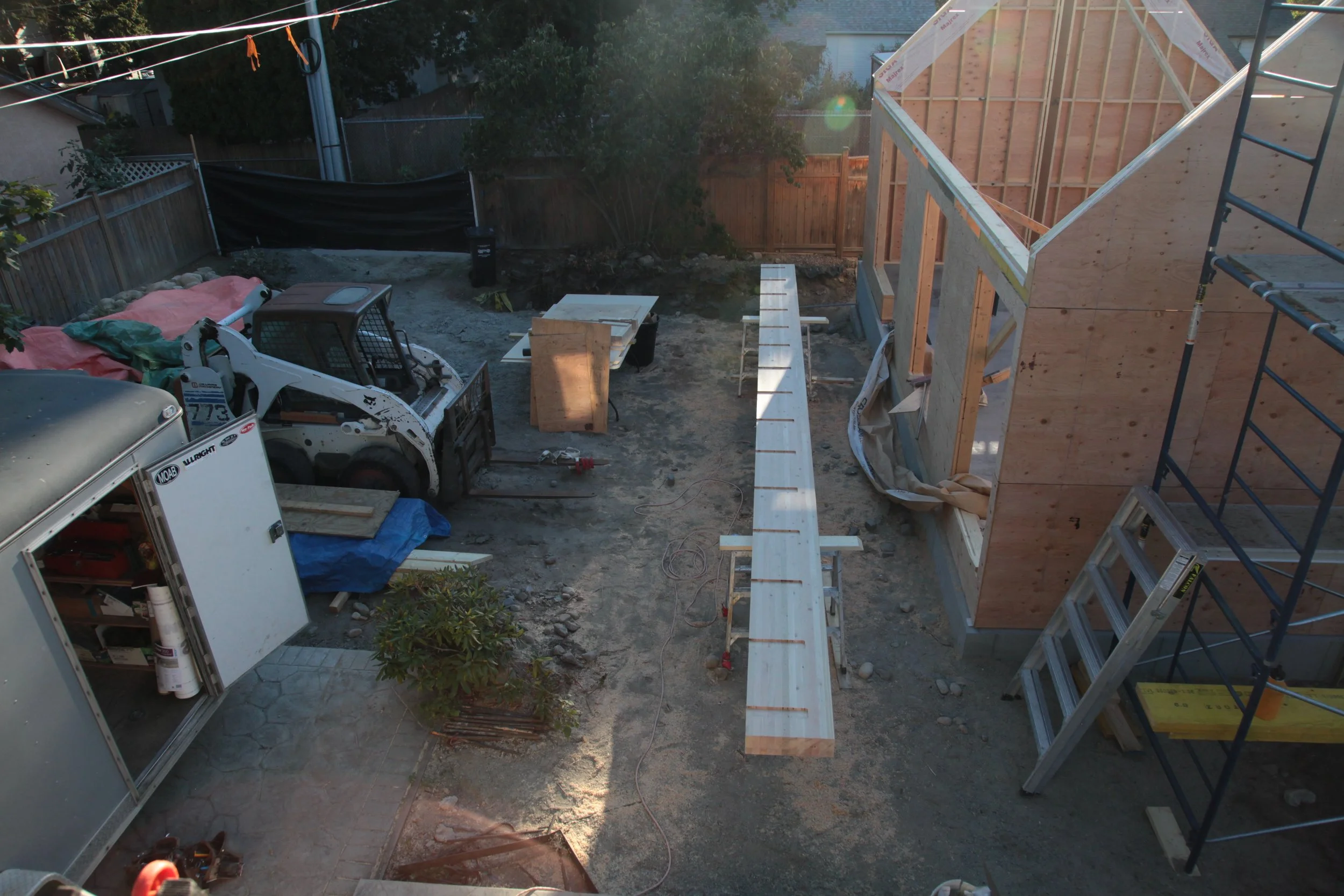
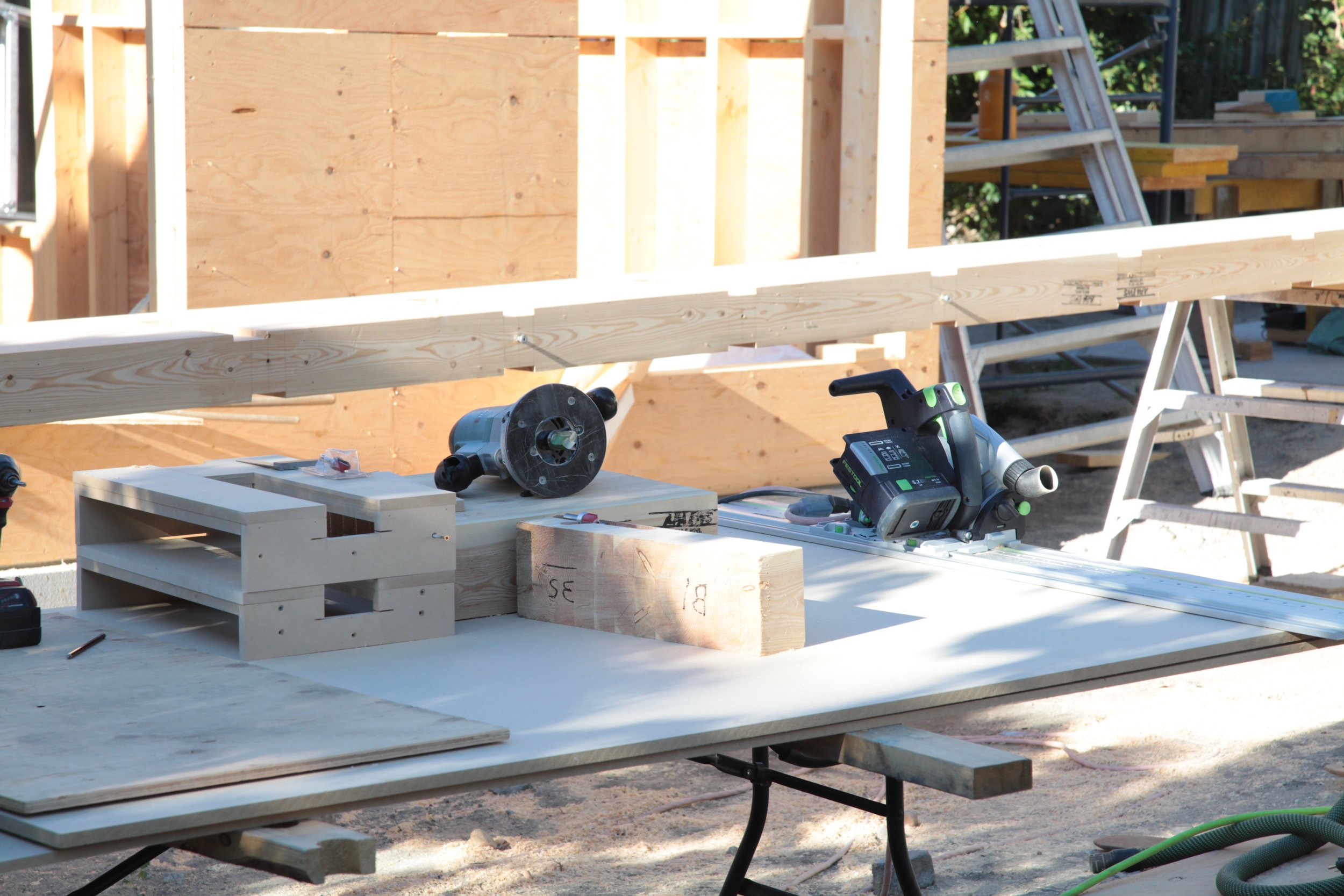
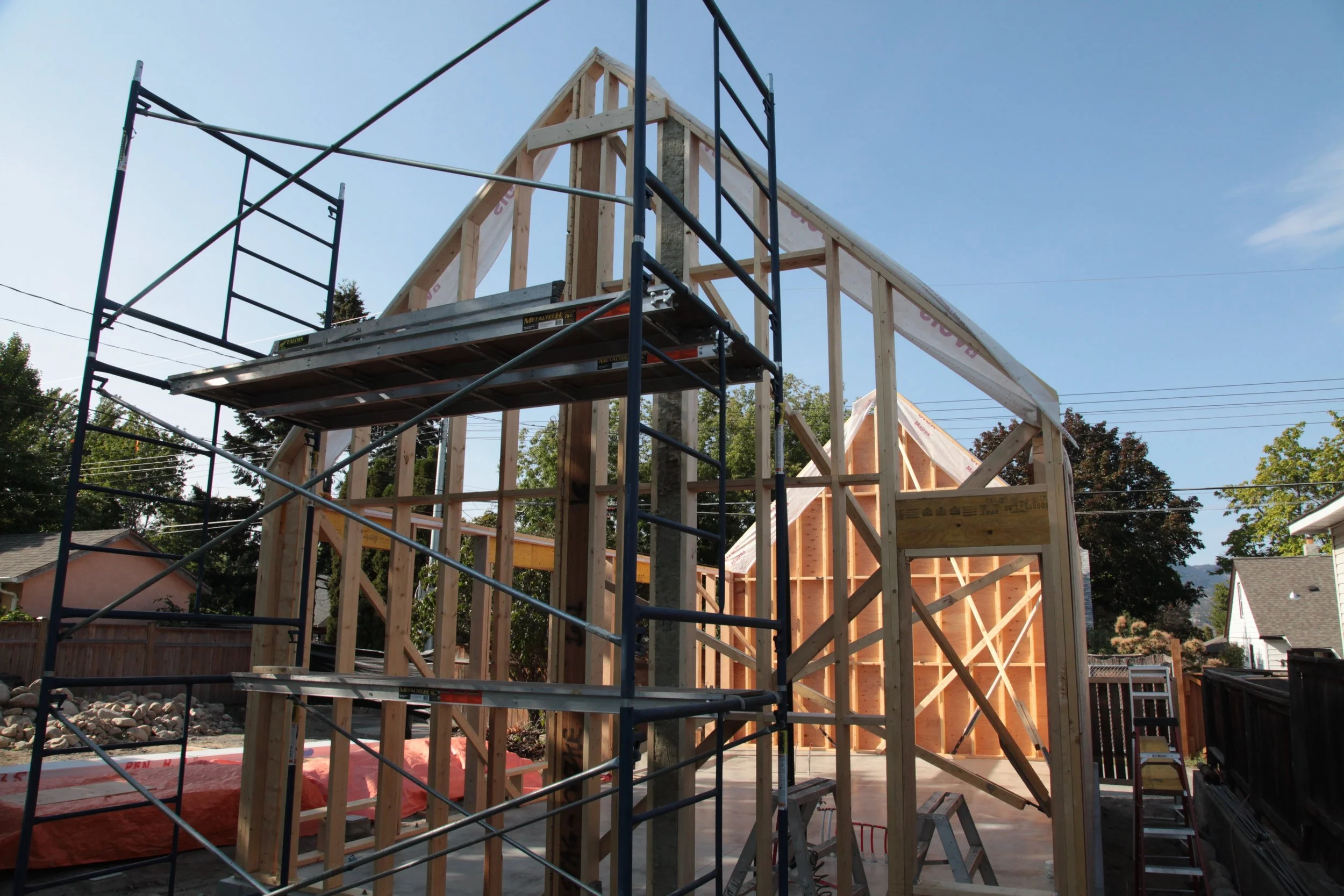
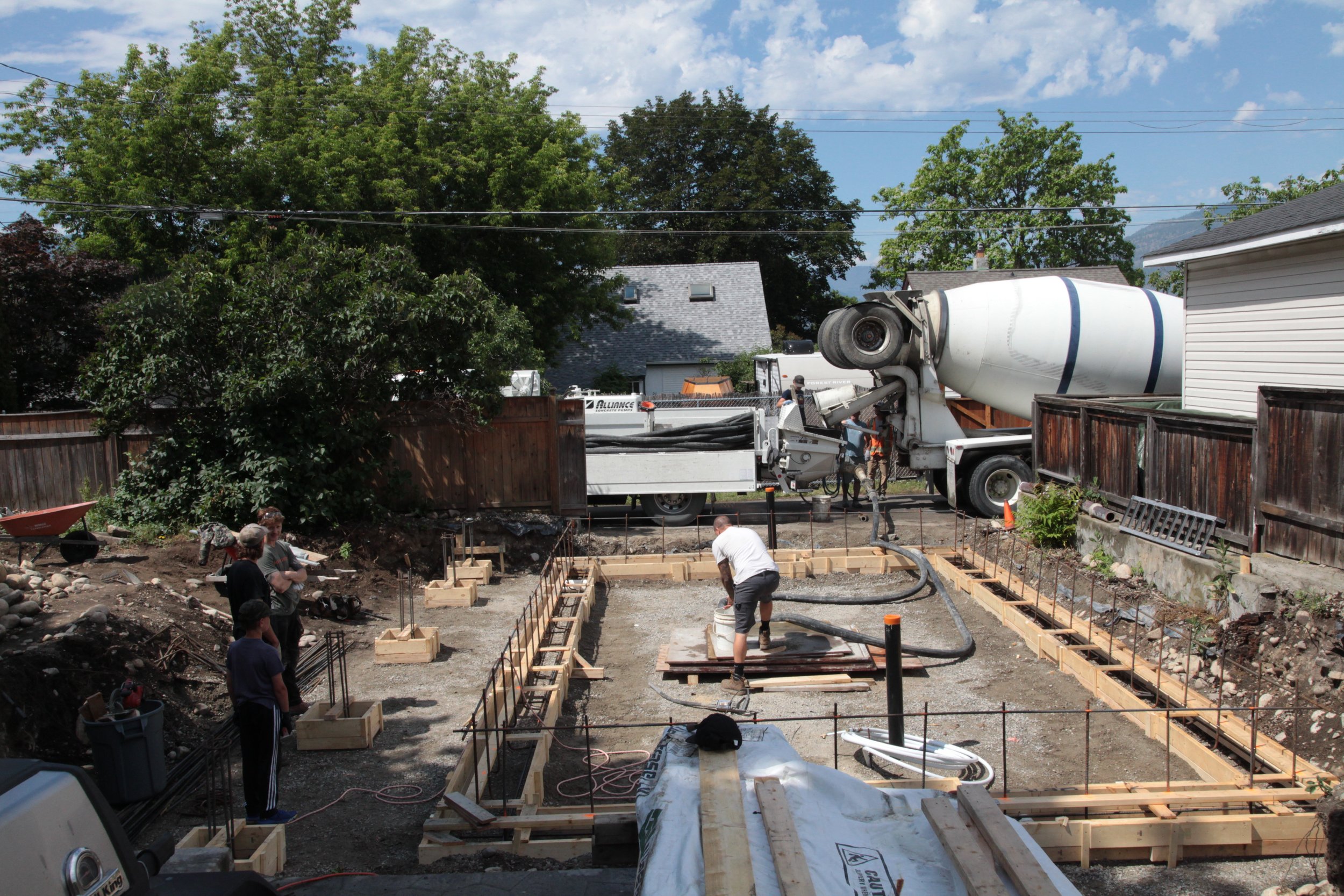
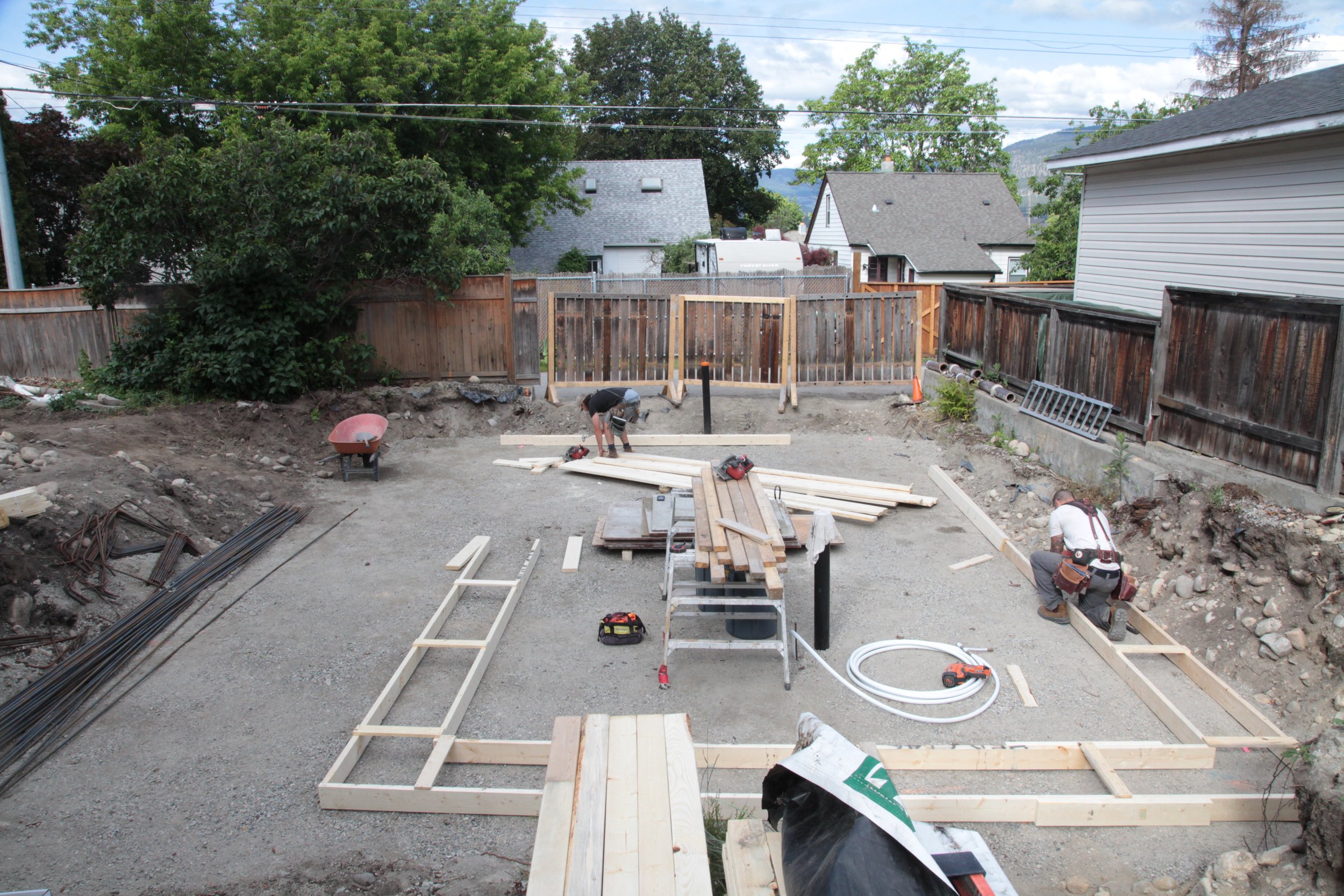
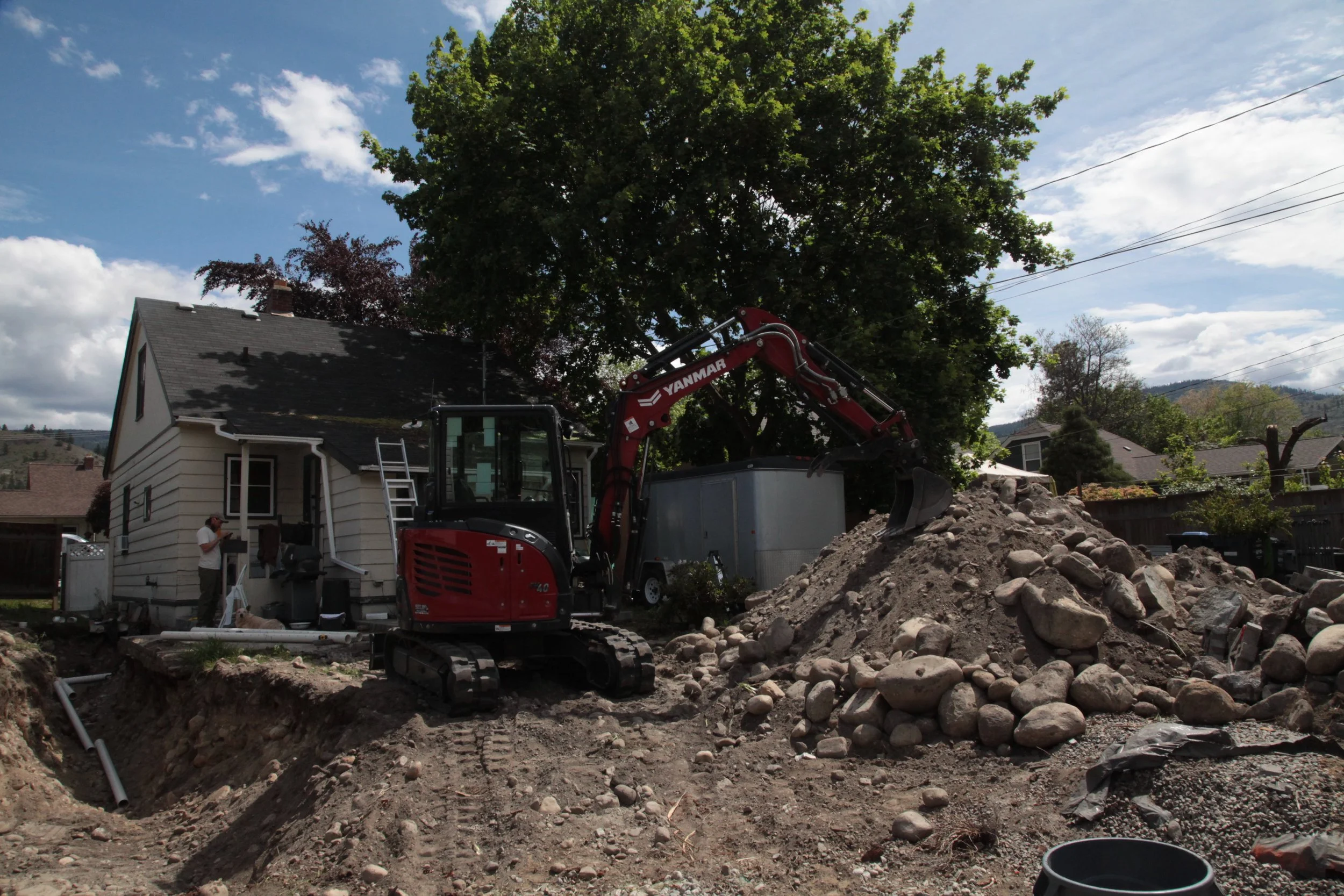
Building Location - Penticton, BC
Architect - Lajoie Architecture
MEW’s Contribution - The rest of it
As the name suggests, this was a personal project. The goal was to build a laneway house that was hyper efficient, cost effective but above all spoke to our general love of carpentry and architecture. The result is Carpenter’s house, a small, detail-orientated, craft-driven, sanity-testing work, spanning two years of evenings, weekends and a parental leave.
Design
With the help of our friend Eric Lajoie of Lajoie Architecture we pared an overcomplicated “L” with a tiered shed roof, into a simple rectangle with a gable roof. The project needed to accept the constraints of a small lot, work within a limited budget and also be conscientious in design and scale of the neighbourhood. The building is orientated to maximize south facing windows and laid out on a 4’ grid to limit material waste. An awning structure was added to the south face, pitched to allow low traveling sunlight to passively heat the interior slab during the winter but also block out high tracking sun in the summer.
Performance
It was important to have a building that could handle the demands of the South Okanagan. The building’s primary heat source is a radiant combi-boiler system supplemented by an electric heat pump that also handles cooling in the summer. An HRV handles interior air movement but passive air flow is achieved with cross ventilating windows. Walls are insulated with R24 rockwool batts and a smart air barrier system was used in conjunction with flexible performance tapes to achieve sub 1.0 air exchanges. The building was wrapped entirely in a peel and stick exterior smart barrier before 8” of eps was added to the roof and 2” of r6 comfortboard was added to the exterior walls. Before the cladding was applied, the walls and roof were strapped and cross-strapped to allow unrestricted air flow over all faces of building. The house lands solidly in Step 4 of the BC Step Code.
Craft
The more subtle detailing was the hardest to achieve. For example, with the exemption collar tie bolts there are no visible fasteners in the whole timber assembly both interior and exterior. This was accomplished with a combination of router cuts, doweled joinery, concealed engineered straps and an unhealthy amount of planning and drafting. The interior nods to minimalism; which always seems to require maximum effort. Flush baseboards, handle-less cabinetry, and the strict awareness of the building grid insure all sight lines speak to this simplicity in aesthetic.
Budget
It’s rude talk about money, but sufficed to say there wasn’t alot of it at any point in this project. To cut costs we relied on two main factors; planning and minimal outsourcing of labour. From ground works to painting and everything in between, there were few things that weren’t accomplished by us and a few dedicated friends and family. In the end, we were still over budget but you can’t put a price on learned experience.
Learning
Our biggest take away was experiencing the build from all 4 cornerstone perspectives. That is designer, builder, tradesmen, and client - the holy tetrad of building. We were simultaneously drowning by construction detailing, stressed by the pressure to execute a build on time and on budget, sore from doing all the work, and overwhelmed by the quantity and monetary weight of decisions. But because of that, it shed a huge amount of perspective on the individual value of each cornerstone and the importance of a cohesive vision from start to finish.